Керамика
Алуминиевата керамика е вид износоустойчив, устойчив на корозия и високоякостен керамичен материал. Тя се използва широко и в момента е най-широко използваната категория високотемпературна структурна керамика. За да се осигури масово производство и да се отговорят на изискванията за равномерен външен вид на продукта, малко количество смилане и лесно фино смилане, е много важно да се избере методът на формоване чрез сухо пресоване. Компресионното формоване изисква заготовката да е прах с определена градация, с по-малко влага и свързващо вещество. Следователно, суспензията от сместа след топково смилане и фино раздробяване трябва да се изсуши и гранулира, за да се получи прах с по-добра течливост и по-висока обемна плътност. Гранулирането чрез сушене чрез пулверизиране се е превърнало в основен метод за производство на строителна керамика и нова керамика. Прахът, приготвен по този процес, има добра течливост, определено съотношение на големи и малки частици и добра обемна плътност. Следователно, сушенето чрез пулверизиране е най-ефективният метод за приготвяне на сухо пресован прах.
Сушенето чрез разпръскване е процес, при който течните материали (включително суспензия) се атомизират и след това се превръщат в сухи прахообразни материали в гореща сушилна среда. Материалите се атомизират в изключително фини сферични капки мъгла. Тъй като капките мъгла са много фини и съотношението на повърхността към обема е много голямо, влагата се изпарява бързо и процесите на сушене и гранулиране се извършват мигновено. Размерът на частиците, съдържанието на влага и обемната плътност на материалите могат да се контролират чрез регулиране на параметрите на сушене. Чрез технология за сушене чрез разпръскване може да се получи сферичен прах с еднакво качество и добра повторяемост, като по този начин се съкращава производственият процес на праха, улеснява се автоматичното и непрекъснато производство и се превръща в ефективен метод за мащабно производство на фини алуминиево-керамични сухи прахообразни материали.
2.1.1 Приготвяне на суспензия
Първокласният индустриален алуминиев оксид с чистота 99% се добавя с около 5% добавки, за да се получи 95% порцеланов материал, а топковото смилане се извършва в съотношение материал: топка: вода = 1:2:1, като се добавят свързващо вещество, дефлокулант и подходящо количество вода, за да се получи стабилна суспензия. Относителният вискозитет се измерва с обикновен разходомер, за да се определи подходящото съдържание на твърди частици в калта, видът и дозата на дефлокуланта.
2.1.2 Процес на сушене чрез пулверизиране
Основните параметри на процеса на управление при сушене чрез разпръскване са: а). Температура на изхода на сушилнята. Обикновено се контролира на 110℃. б). Вътрешен диаметър на дюзата. Използвайте отвор 0,16 мм или 0,8 мм. в). Разлика в налягането на циклонния сепаратор, контролирана на 220 Pa.
2.1.3 Проверка на производителността на праха след сушене чрез пулверизиране
Определянето на влажността се извършва съгласно общоприетите методи за определяне на влажността на керамичните материали. ЧастицитеМорфологията и размерът на частиците бяха наблюдавани с микроскоп. Течливостта и обемната плътност на праха са тествани съгласно експерименталните стандарти на ASTM за течливост и обемна плътност на металния прах. Методът е: при условие на липса на вибрации, 50 g прах (с точност до 0,01 g) преминава през стъклена фуния с диаметър 6 mm и дължина 3 mm за неговата течливост; при условие на липса на вибрации, прахът преминава през същата стъклена фуния и пада в контейнер с височина 25 mm от същата стъклена фуния. Невибриращата плътност е плътността на рохкавата опаковка.
3.1.1 Приготвяне на течен разтвор
При процеса на гранулиране чрез сушене чрез разпръскване, подготовката на суспензията е от решаващо значение. Съдържанието на твърди вещества, фиността и течливостта на калта ще повлияят пряко върху добива и размера на частиците на сухия прах.
Тъй като прахът от този вид алуминиев порцелан е безплоден, е необходимо да се добави подходящо количество свързващо вещество, за да се подобри формообразуването на заготовката. Често използвани органични вещества като декстрин, поливинилов алкохол, карбоксиметилцелулоза, полистирен и др. В този експеримент е избран поливинилов алкохол (PVA), водоразтворимо свързващо вещество. Той е по-чувствителен към влажността на околната среда, като промяната на влажността на околната среда значително ще повлияе на свойствата на сухия прах.
Поливиниловият алкохол има много различни видове, различни степени на хидролиза и степен на полимеризация, което ще повлияе на процеса на сушене чрез разпръскване. Неговата обща степен на хидролиза и степен на полимеризация ще повлияят на процеса на сушене чрез разпръскване. Дозировката му обикновено е 0,14 - 0,15 тегл.%. Добавянето на твърде много ще доведе до образуването на твърди, сухи прахообразни частици от праха за гранулиране чрез разпръскване, предотвратявайки деформацията на частиците по време на пресоване. Ако характеристиките на частиците не могат да бъдат отстранени по време на пресоване, тези дефекти ще се съхранят в зеления материал и няма да могат да бъдат отстранени след изпичане, което ще повлияе на качеството на крайния продукт. Твърде малкото добавяне на свързващо вещество ще увеличи загубите по време на работа. Експериментът показва, че когато се добави правилно количество свързващо вещество, сечението на зеления материал се наблюдава под микроскоп. Може да се види, че когато налягането се увеличи от 3Mpa до 6Mpa, сечението се увеличава плавно и има малък брой сферични частици. Когато налягането е 9Mpa, сечението е гладко и на практика няма сферични частици, но високото налягане ще доведе до стратификация на зелената заготовка. PVA се отваря при около 200 ℃.
Започва да гори и се оттича при около 360 ℃. За да се разтвори органичното свързващо вещество и да се намокрят частиците на заготовката, да се образува течен междинен слой между частиците, да се подобри пластичността на заготовката, да се намали триенето между частиците и триенето между материалите и матрицата, да се насърчи увеличаването на плътността на пресованата заготовка и хомогенизирането на разпределението на налягането, а също така се добавя подходящо количество пластификатор, като обикновено се използват глицерин, етил оксалова киселина и др.
Тъй като свързващото вещество е органичен макромолекулен полимер, методът на добавяне на свързващото вещество към суспензията също е много важен. Най-добре е приготвеното свързващо вещество да се добави към еднородната кал с необходимото съдържание на твърдо вещество. По този начин може да се избегне попадането на неразтворени и недиспергирани органични вещества в суспензията и да се намалят евентуалните дефекти след изпичане. Когато се добави свързващото вещество, суспензията лесно се генерира чрез топково смилане или разбъркване. Въздухът, обвит в капката, е в сухия прах, което прави сухите частици кухи и намалява обемната плътност. За да се реши този проблем, могат да се добавят пеногасители.
Поради икономически и технически изисквания е необходимо високо съдържание на твърди вещества. Тъй като производственият капацитет на сушилнята се отнася до изпаряващата се вода на час, суспензията с високо съдържание на твърди вещества значително ще увеличи добива на сух прах. Когато съдържанието на твърди вещества се увеличи от 50% на 75%, производителността на сушилнята ще се увеличи два пъти.
Ниското съдържание на твърди частици е основната причина за образуването на кухи частици. В процеса на сушене водата мигрира към повърхността на капката и носи твърди частици, което прави вътрешната част на капката куха; ако около капката се образува еластичен филм с ниска пропускливост, поради ниската скорост на изпаряване, температурата на капката се повишава и водата се изпарява от вътрешната част, което прави капката издута. И в двата случая кълбовидната форма на частиците ще бъде разрушена и ще се получат кухи пръстеновидни или ябълковидни или крушовидни частици, което ще намали течливостта и обемната плътност на сухия прах. Освен това, суспензията с високо съдържание на твърди частици може да намали...
При кратък процес на сушене, намаляването на процеса на сушене може да намали количеството лепило, пренесено върху повърхността на частиците заедно с водата, така че да се избегне по-голяма концентрация на свързващо вещество върху повърхността на частиците, отколкото в центъра, така че частиците да имат твърда повърхност и частиците да не се деформират и смачкват по време на процеса на пресоване и формоване, като по този начин се намалява масата на заготовката. Следователно, за да се получи висококачествен сух прах, съдържанието на твърди вещества в суспензията трябва да се увеличи.
Суспензията, използвана за спрей сушене, трябва да е достатъчно течлива и с възможно най-малко влага. Ако вискозитетът на суспензията се намали чрез въвеждане на повече вода, не само се увеличава консумацията на енергия за сушене, но и се намалява обемната плътност на продукта. Следователно е необходимо да се намали вискозитетът на суспензията с помощта на коагулант. Изсушената суспензия е съставена от няколко микрона или по-малки частици, които могат да се разглеждат като колоидна дисперсионна система. Теорията за колоидната стабилност показва, че върху частиците на суспензията действат две сили: сила на ван дер Ваалс (сила на Кулон) и сила на електростатично отблъскване. Ако силата е главно гравитационна, ще възникнат агломерация и флокулация. Общата потенциална енергия (VT) на взаимодействието между частиците е свързана с разстоянието между тях, по време на което VT в даден момент е сума от гравитационната енергия VA и енергията на отблъскване VR. Когато VT между частиците представлява максимална положителна потенциална енергия, това е система за деполимеризация. За дадена суспензия VA е определена, така че стабилността на системата се определя от функциите, които контролират VR: повърхностния заряд на частиците и дебелината на двойните електрически слоеве. Дебелината на бислоя е обратно пропорционална на корен квадратен от валентната връзка и концентрацията на равновесния йон. Компресията на двойния слой може да намали потенциалната бариера на флокулацията, така че валентната връзка и концентрацията на равновесните йони в разтвора трябва да бъдат ниски. Най-често използваните деемулгатори са HCI, HNO3, NaOH, (CH)3noh (кватернерен амин), GA и др.
Тъй като водната суспензия от керамичен прах от алуминиев оксид 95 е неутрална и алкална, много коагуланти, които имат добър разреждащ ефект върху други керамични суспензии, губят своята функция. Следователно е много трудно да се приготви суспензия с високо съдържание на твърди вещества и добра течливост. Безплодната алуминиева суспензия, която принадлежи към амфотерния оксид, има различни процеси на дисоциация в киселинна или алкална среда и образува дисоциационен статус с различен състав и структура на мицелите. Стойността на pH на суспензията ще повлияе пряко върху степента на дисоциация и адсорбция, което ще доведе до промяна на ζ потенциала и съответната флокулация или дисоциация.
Алуминиевата суспензия има максимална стойност на положителен и отрицателен ζ потенциал в киселинна или алкална среда. В този момент вискозитетът на суспензията е в най-ниската стойност на състояние на декоагулация, докато когато суспензията е в неутрално състояние, вискозитетът ѝ се увеличава и настъпва флокулация. Установено е, че течливостта на суспензията се подобрява значително и вискозитетът ѝ се намалява чрез добавяне на подходящ деемулгатор, така че стойността на вискозитета ѝ е близка до тази на водата. Течливостта на водата, измерена с обикновен вискозиметър, е 3 секунди / 100 мл, а течливостта на суспензията е 4 секунди / 100 мл. Вискозитетът на суспензията се намалява, така че съдържанието на твърди вещества в суспензията може да се увеличи до 60% и да се образува стабилна пълнеж. Производственият капацитет на сушилнята се отнася до изпаряването на водата на час, така че и суспензията.
3.1.2 Контрол на основните параметри в процеса на сушене чрез пулверизиране
Моделът на въздушния поток в сушилната кула влияе върху времето за сушене, времето на задържане, остатъчната вода и залепването на капките по стените. В този експеримент процесът на смесване на капките с въздух е смесен поток, т.е. горещият газ навлиза в сушилната кула отгоре, а пулверизиращата дюза е монтирана в долната част на сушилната кула, образувайки фонтанна струя, а капката е парабола, така че смесването на капката с въздуха е противоток и когато капката достигне върха на хода, тя се превръща в поток надолу по течението и пръска в конична форма. Веднага щом капката влезе в сушилната кула, тя скоро ще достигне максималната скорост на сушене и ще влезе в етап на сушене с постоянна скорост. Продължителността на етапа на сушене с постоянна скорост зависи от съдържанието на влага в капката, вискозитета на калта, температурата и влажността на сухия въздух. Граничната точка C от етапа на сушене с постоянна скорост до етапа на бързо сушене се нарича критична точка. В този момент повърхността на капката вече не може да поддържа наситено състояние чрез миграция на вода. С намаляването на скоростта на изпарение температурата на капките се повишава и повърхността на капките в точка D се насища, образувайки слой от твърда обвивка. Изпарението се премества навътре и скоростта на изсушаване продължава да намалява. По-нататъшното отстраняване на вода е свързано с влагопропускливостта на твърдата обвивка. Следователно е необходимо да се контролират разумните работни параметри.
Съдържанието на влага в сухия прах се определя главно от температурата на изхода на спрей сушилнята. Съдържанието на влага влияе върху обемната плътност и течливостта на сухия прах и определя качеството на пресованата заготовка. PVA е чувствителен към влажност. При различни условия на съдържание на влага, едно и също количество PVA може да причини различна твърдост на повърхностния слой на частиците сух прах, което води до колебания в определянето на налягането и нестабилност на качеството на продукцията по време на процеса на пресоване. Следователно, температурата на изхода трябва да се контролира стриктно, за да се гарантира съдържанието на влага в сухия прах. Обикновено температурата на изхода трябва да се контролира на 110 ℃, а температурата на входа трябва да се регулира съответно. Температурата на входа не трябва да надвишава 400 ℃, като обикновено се контролира на около 380 ℃. Ако температурата на входа е твърде висока, температурата на горещия въздух на върха на кулата ще прегрее. Когато капките мъгла се издигнат до най-високата точка и попаднат в прегрят въздух, върху керамичния прах, съдържащ свързващо вещество, ефектът на свързващото вещество ще бъде намален и накрая ще се повлияе на производителността на пресоване на сухия прах. Второ, ако входната температура е твърде висока, това също ще повлияе на експлоатационния живот на нагревателя, а обвивката на нагревателя ще падне и ще навлезе в сушилната кула с горещ въздух, замърсявайки сухия прах. При условие, че входната и изходната температура са основно определени, изходната температура може да се регулира и чрез налягането на захранващата помпа, разликата в налягането на циклонния сепаратор, съдържанието на твърди вещества в суспензията и други фактори.
Разлика в налягането на циклонния сепаратор. Разликата в налягането на циклонния сепаратор е голяма, което ще увеличи температурата на изхода, ще увеличи събирането на фини частици и ще намали добива на сушилнята.
3.1.3 Свойства на прах, изсушен чрез пулверизиране
Течливостта и плътността на опаковката на алуминиево-керамичния прах, приготвен чрез метод на спрей сушене, обикновено са по-добри от тези, приготвени по обичайния процес. Прахът, получен чрез ръчно гранулиране, не може да преминава през детекторното устройство без вибрации, а прахът, получен чрез спрей гранулиране, може да го направи напълно. В съответствие със стандарта ASTM за изпитване на течливостта и насипната плътност на метални прахове, бяха измерени насипната плътност и течливостта на частиците, получени чрез спрей сушене при различни условия на водно съдържание. Вижте Таблица 1.
Таблица 1 Плътност на насипно състояние и течливост на прах, изсушен чрез пулверизиране
Таблица 1 Плътност и дебит на праха
Съдържание на влага (%) | 1.0 | 1.6 | 2.0 | 2.2 | 4.0 |
Плътност на херметичността (g/cm)3) | 1.15 | 1.14 | 1.16 | 1.18 | 1.15 |
Ликвидност (и) | 5.3 | 4.7 | 4.6 | 4.9 | 4.5 |
Съдържанието на влага в праха, изсушен чрез пулверизиране, обикновено се контролира на 1-3%. В този момент течливостта на праха е добра, което може да отговори на изискванията за пресоване.
DG1 е плътността на ръчно приготвения гранулиращ прах, а DG2 е плътността на праха за спрей гранулиране.
Ръчно гранулираният прах се приготвя чрез топково смилане, сушене, пресяване и гранулиране.
Таблица 2 Плътност на пресовани прахове, образувани чрез ръчно гранулиране и гранулиране чрез пулверизиране
Таблица 2 Плътност на зеленото тяло
Налягане (МПА) | 4 | 6 | 8 | 10 | 12 | 14 |
DG1 (г/см3) | 2.32 | 2.32 | 2.32 | 2.33 | 2.36 | 2.4 |
DG2 (g/cm3) | 2.36 | 2.46 | 2.53 | 2.56 | 2.59 | 2.59 |
Размерът на частиците и морфологията на праха бяха наблюдавани чрез микроскоп. Вижда се, че частиците са основно твърди, сферични, с ясна граница на разделяне и гладка повърхност. Някои частици са с форма на ябълка, круша или мостовидни, което представлява 3% от общия брой. Разпределението на размера на частиците е следното: максималният размер на частиците е 200 μm (< 1%), минималният размер на частиците е 20 μm (единичен), повечето частици са около 100 μm (50%), а повечето частици са около 50 μm (20%). Прахът, получен чрез спрей сушене, се синтерова при 1650 градуса, а плътността му е 3170 g/cm.3.
(1) 95 алуминиева суспензия с 60% съдържание на твърдо вещество може да се получи чрез използване на PVA като свързващо вещество, добавяне на подходящ коагулант и лубрикант.
(2) разумен контрол на параметрите на операцията по сушене чрез разпръскване може да доведе до получаване на идеален сух прах.
(3) чрез прилагане на процес на сушене чрез разпрашване може да се получи алуминиев прах 95, подходящ за сухо пресоване в насипно състояние. Неговата свободна плътност е около 1,1 g/cm3и плътността на синтероване е 3170 g/cm3.
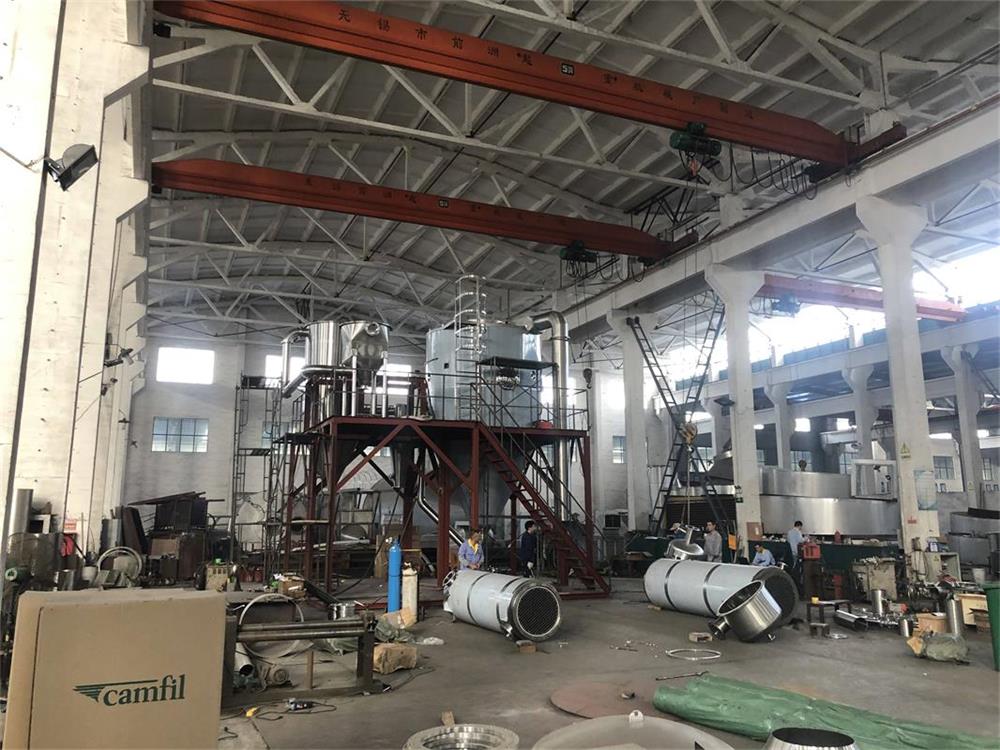
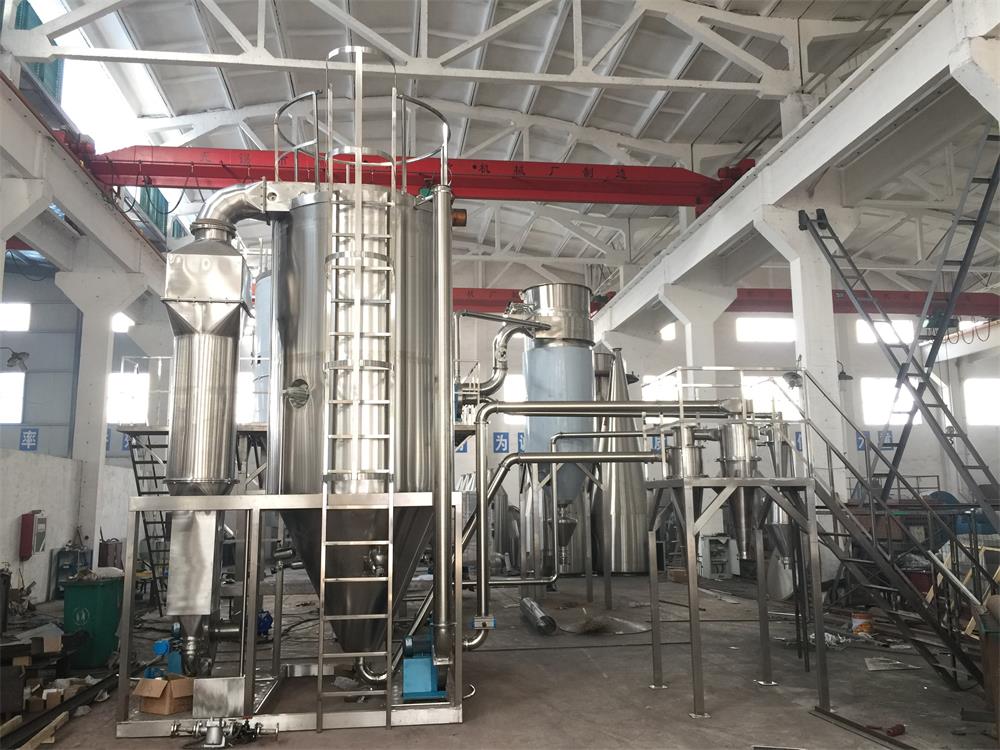